【2025年最新版】生産スケジューラーとは?実際の運用を通して感じた中小製造業におけるスケジューリングとその意外な落とし穴

生産管理は製造業の成功に不可欠な要素であり、近年多くの企業にて活用が進んでいるシステムの1つに生産スケジューラーがあります。
このプロセスは、リソースを効率的に配分し、生産の効率化とコスト削減を実現するための重要なツールとして認識されています。
しかし、生産スケジューラーには予想外の落とし穴も存在します。
本記事では、スケジューラーの概要とそのメリット、そしてスケジューリングに潜む意外な落とし穴とその対策について探ります。
生産スケジューラーとは?
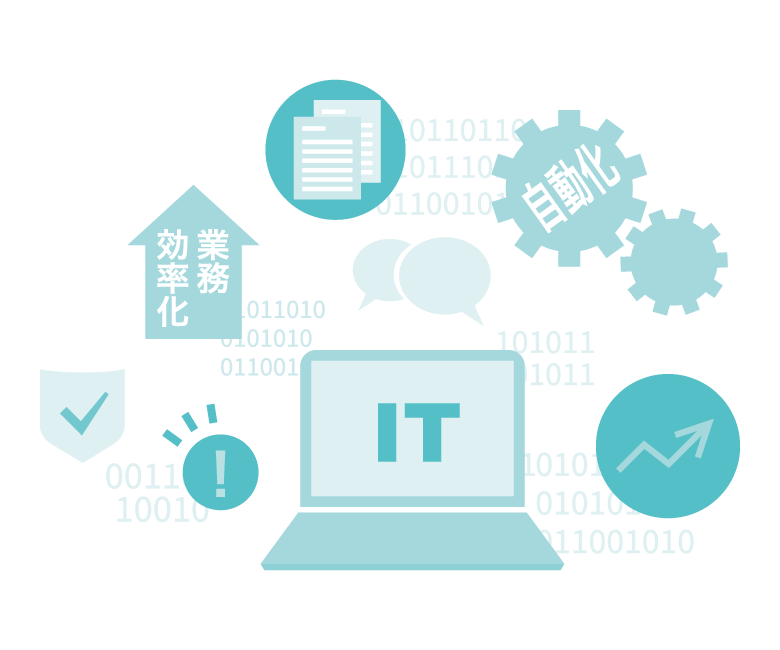
生産管理は製造業の核心をなすプロセスであり、生産スケジューリングはその中心的な要素として取り扱われることの多いテーマです。
生産スケジューリングは、製造プロセスの効率化、コスト削減、納期遵守を目指し、資源の最適な配分を図るために不可欠なツールとされています。
その導入には以下のような効果が謳われることが多いです。
生産効率の向上
時間管理の最適化: 各工程の時間を効率的に計画し、全体の生産プロセスを最適化します。
リードタイムの短縮: 生産工程のスムーズな進行により、製品の生産から出荷までの時間を短縮できます。
リソースの効果的な利用
有限能力スケジューリング: キャパシティを考慮した計画を立てることで、リソースを無駄なく活用できます。
稼働率の最適化: 設備や人員の過不足を防ぎ、効率的にリソースを割り当てることが可能になります。
意思決定の支援
データ駆動型の意思決定: 過去のデータや現在の生産状況を基に、より精度の高い意思決定を行えます。
継続的な改善: 生産実績をシステムにフィードバックし、継続的な改善活動を支援します。
透明性と可視化の向上
生産進捗の透明性: ガントチャート等を用いて生産進捗を可視化し、進捗状況をリアルタイムで把握できます。
情報共有の促進: 部門間での情報共有が容易になり、全員が生産状況を把握できるようになります。
コスト削減
過剰生産の削減: 生産スケジュールの最適化により、過剰生産や在庫過多の問題を削減できます。
効率的な人員配置: 人員を適切に配置し、人件費の最適化を図ることが可能です。
導入により、上記のようなメリットを享受できるといわれています。
お気軽にお問い合わせください。
専門スタッフが無料でご相談を承ります。
TEL 0198-35-7660 平日 10:00~18:00
スケジューリングに潜む意外な落とし穴
しかし、このスケジューリングプロセスは万能ではなく、波があり突発的な変更の多い中小製造業の受注実態と照らし合わせた際に特定の課題と限界を有しています。
むしろスケジューリングへの依存は製造効率を大幅に低下させるといっても過言ではありません。
以下、中小製造業の生産現場で生産スケジューリングを導入した際に直面した主要な問題点を探り、その対策について考察します。
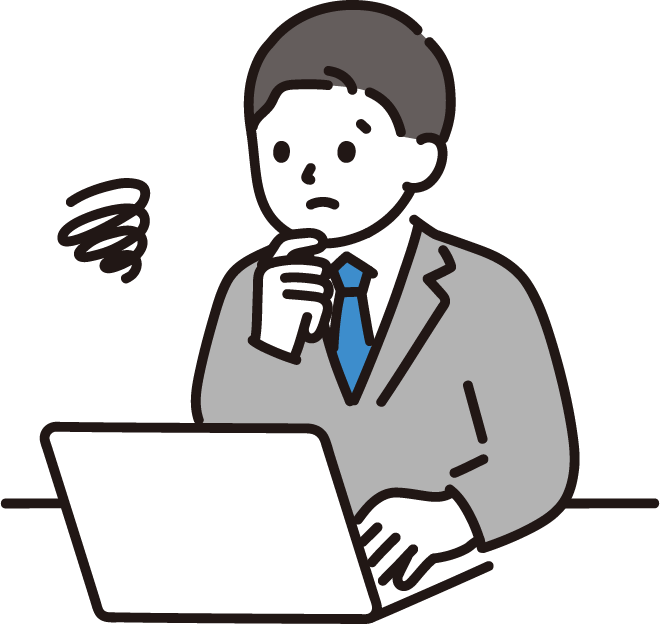
柔軟性の欠如
生産スケジューリングはしばしば静的であり、予期せぬ変更や緊急事態に対して即座に対応する柔軟性を欠くことがあります。例えば、急な注文増加や市場の変動に迅速に対応する必要がある場合、固定化されたスケジュールは逆に障害となり得ます。
飛び込みや特急の多い中小製造業にてスケジューリングを導入する場合、毎日がスケジュールの変更と山崩しの連続となる可能性が高まります。
あくまでも1か月単位で、受注量を調整できることが前提となっているシステムが多いため、中小製造業の受注実態からは大きな乖離があると運用を通し感じています。
複雑さと管理の困難さ
詳細に策定されたスケジュールは、管理が複雑になる傾向があります。複数の部品やプロセスが関与する場合、スケジュールの管理と適時の調整には専門知識と高度な注意力が必要とされ、これが業務の効率性を損なうこともあります。
スケジューラの管理に専属の人員を配置することもしばしばです。
間接業務時間を減らすことが目的のスケジューラーですが、その調整に多くの作業時間を割いてしまうようでは本末転倒です。
過剰な依存
生産スケジューリングツールや自動化に過度に依存することは、現場の直観や経験に基づく柔軟な意思決定を妨げるリスクをはらんでいます。すべての状況がスケジュール通りに進行するわけではなく、場合によっては人間の判断がより適切な対応を導くことがあります。
リソースへの過度な負担
厳格なスケジュールは、従業員や機械への過度な負担を招くことがあります。これは生産効率の低下だけでなく、労働者の疲労や機械の早期劣化につながり、結果的に生産プロセスの持続可能性を損なうことにもなりかねません。
予測の誤り
スケジュールはしばしば過去のデータや市場予測に基づいて策定されますが、これらの予測が常に正確であるとは限りません。誤った予測に基づくスケジュールは、過剰在庫や生産不足といった問題を引き起こす可能性があります。
対策と考察
これらの課題に対処するためには、スケジューリングプロセスにおける柔軟性と現場の意思決定を重視する必要があります。
スケジューラーを使用しないというのも選択肢の1つでしょう。
対策を講じるうえでは、現場のリアルタイムデータを活用した動的なスケジューリング、現場の従業員との連携強化、そして予期せぬ状況への迅速な対応能力の向上が鍵となります。
また、過剰な自動化やツール依存からの脱却も、より柔軟で受注の波、環境の変化に対応できる生産管理を実現するためには不可欠です。
スケジューラーを用いた生産スケジューリングは一見効率よく多くのメリットを提供するかのような印象を受けますが、それに依存することなく、状況に応じた柔軟かつ効率的な対応が実際の生産現場では求められています。
現場の知識と経験を活かし、現場の計測データと生産管理システムをあくまで補助として用いることで、より効果的な生産管理が可能となるでしょう。
総合生産管理システムTEDでは現場からのリアルタイムの進捗データを収集し、柔軟な生産計画を提案、運用していく仕組みを備えています。
多くの生産管理システムの導入運用、またその失敗を経験し、そこから生じた改善策を詰め込み開発した生産管理システムをぜひ一度ご検討ください。
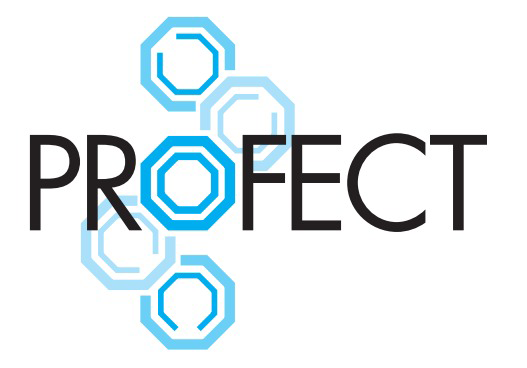
お気軽にお問い合わせください。
専門スタッフが無料でご相談を承ります。
TEL 0198-35-7660 平日 10:00~18:00
コメント