【2025年最新版】生産管理とは?中小製造業向けに目的や内容を徹底解説!

ものが売れる時代から売れない時代へ
「作れば売れる時代」、「単純にコストに希望の利益を乗せれば良かった時代」、今から思えばかつて夢のような時代がありました。そんな少品種大量生産の時代は、右から左へ注文を流すだけですべて良し、いちいち細かな管理なんてする必要はありませんでした。ただ、指示を出し、現場をあおっていれば万事オッケーでした。
今はどうでしょう。「ものが売れない時代」、「販売価格は市場が決めるコスト競争力勝負の時代」となりました。必需品が市場に行き渡り、消費者の好みが多様かつ細分化されました。今を勝ち残るためには、市場に商品を素早く送り届け、多品種少量・短納期生産を行うことが必要不可欠となっています。
他者を凌駕する技術を持って市場を占有するのも、今を生きる一つの選択肢であるのには違いありません。しかし、残念ながら、絶えまない技術革新を中小企業が維持できるかは疑問です。3Dプリンターのような最新技術にあっという間に駆逐される恐れもあります。
では、この時代に、製造業はどのように変化すべきでしょうか。かつての「売れる時代の成功体験よ、もう一度!」と願っていても、もうその時代は戻って来ません。大変革の渦の真っただ中、昔ながらのやり方を続けていては、あっという間にライバルの後塵を拝することになってしまいます。変わりゆく環境や状況を素早く捉えて、課題解決の対策をいち早く打たねば生き残ることはできません。
まだ昭和のKKDに頼るの?
KKDという言葉は、皆さんご存知のことと思います。「経験」「勘」「度胸」の頭文字を取った言葉で、日本の製造業では古くからKKDが尊重されてきました。何かトラブルが起こった時に、長年の経験と勘によってその原因と解決策を見つけ、度胸によって改善策を実行します。ものづくり大国であった日本において、職人技と言われる素晴らしい技術は、経験、勘、度胸の賜物と言っても良いでしょう。
それを否定するつもりはありません。昔はそれで良かったのです。データの裏付けなんかなくても、経験を積める時間より変化周期の方が長かった時代は、KKDでなんとか乗り切れました。「今までこのやり方でうまく行っていたのだから今度も大丈夫だろう」、「多分これでうまく行くだろう」、「えいや!でやってしまおう」。皆さまも思い当たる節はありませんか。
しかしながら、ものが売れる時代から売れない時代へ変化する中、従来のKKDだけで工場運営や経営判断を続けられないことは明白です。KKDでは人によって判断が変わってしまいます。いわゆる属人化による弊害です。また、今まで経験したことのない状況に直面した時には、思考がフリーズしてしまう可能性があります。そして世代交代が起きたとき、蓄積されたノウハウがなくなってしまうのです。
興味深いことに、最近は「古いKKD」の進化形として「新しいKKD」が注目されています。新しいKKDとは、「仮説」「検証」「データ」です。人の勘や経験だけに頼るのでなく、データを活用してPDCAサイクルを回すことによって、より成功率の高い改善策を導くことができます。これからは、古いKKDだけに頼るのではなく、新しいKKDとともに両輪で活用していくことが求められます。
よりきめ細かな管理が求められる時代
「売上が上がっていれば問題はないだろう」。これも一種の勘に頼る経営ではないかと思います。本当に売上が増えていれば問題はないのでしょうか?「売上が七難隠す」という言葉があります。売上が増加している一方で、知らないうちに経費が増加して利益が減少し、赤字に陥ることはよくあることです。
売上高に重点を置いた目標は、どちらかと言うと市場や社会が右肩上がりに成長しているときに有効です。もちろん売上増加はチャレンジすべき大切な目標ではありますが、それだけでは現在は通用しません。売上高のような絶対額重視の経営から、利益を重視する経営へ舵を切り直す必要があります。なぜなら、売上増加は一朝一夕では達成できませんが、利益率の改善は自社内における様々な創意工夫で比較的短期間で実現できるからです。
例えば、同じ年商10億円でも、粗利率が0.1%違えば売上総利益は1000万円の差となって現れます。これは大きいですよね。0.1%、いや0.01%にこだわるべきです。その粗利を稼ぐためには、受注管理、原価管理、製造管理、進捗管理、品質管理、在庫管理などのあらゆる管理にいっそうの緻密さが求められます。いわゆる「成り行きの管理」では、他社に勝るコスト競争力を付けることはできません。
高コスト企業は一般的に、高人件費、低生産性、低歩留まり、設備稼動率の低さ、間接人員の多さなどに原因があるとされますが、その根本原因は「管理の質と量の弱さ」にあると言えます。製品ごとの利益に目を光らせることが利益重視の基本戦略であり、そのためにはすべての取引において、今までになかったきめ細かい管理が必要となります。そこで重要なのが生産管理のDXです。DXによって生産管理のメッシュを細くし、ムダを減らし、企業の基礎体力を徹底的に改善し、真のコスト競争力を付けることが儲けを生む最大の近道になります。
そもそも生産管理とは?
それでは生産管理とは具体的にどのようなことをするのか見ていきましょう。まず、生産管理に関するJIS(日本工業規格)の定義です。日本規格協会のJIS Z8141 番号1215:2001によると、「財・サービスの生産に関する管理活動」を指し、以下の内容になります。
具体的には、所定の品質Q (quality)・原価C (cost)・数量及び納期D (delivery) で生産するため、又はQ・C・Dに関する最適化を図るため、人、物、金、情報を駆使して、需要予測、生産計画、生産実施、生産統制を行う手続き及びその活動。狭義には、生産工程における生産統制を意味し、工程管理ともいう。
日本規格協会 JIS Z8141 番号1215:2001
このように業界標準的な定義を記載しても、「それで生産管理って何をすることなの?」という方もおられるでしょう。生産管理とは、その名の通り、生産に関する “入” (受注)から “出”(出荷) までの工程全般を統括的に管理することです。その肝はQCDの最適化にあり、改善活動でQCDをどのように高いレベルでバランスさせるかにあります。管理の対象もここに集約されます。
■QCDの一般的な定義と管理上の注意点
Q(品質) | C(コスト) | D(納期) | |
一般的な定義 | 製品の品質合格ラインを決め、徹底する 顧客の求めている品質という視点が重要 合格ラインに満たない製品に関しては改善を加えていく、不良品として出荷しないことも | 人的、金銭的コストを基にして、定められた品質や納期を達成する予算を立てる 原材料費や人件費といったコストに変動がある場合、予算をオーバーしないようコストの改善を行う | 出荷までの生産工程を明確にし、工数・時間を算出した上でスケジュールを立てる 進行がスケジュール通りに行われているかを常に確認し、納期に間に合うように調整・改善を行う |
管理上の注意点 | ものだけではなく、業務プロセス全体の品質を管理する | 間接業務、見えない業務のムリ、ムラ、ムダも管理する | 業務全体の時間や設備の稼働状況等も管理する |
4MとQCDを意識した生産管理
ところで皆さまは、正確に自社のQCDを把握できているでしょうか。お客さまから評価されているのは、QCDのどの部分なのでしょう。QCDは製造業にとっての付加価値の源泉です。自社の強み・弱みを把握するうえで、QCDに注目して自社の業務を棚卸ししてみましょう。生産管理の前提として、まず自社のQCDを製品別に把握できていなければなりません。
そして、QCDは生産活動の結果であり、その結果を生み出すのは「生産の4M」だという点が重要です。「生産の4M」とは、 Man(作業者)、Machine(機械・設備)、Material(資材・仕掛)、Method(しくみ・システム)で構成され、生産活動に必要な4つの要素を指しています。4Mは生産に必要なインプットのアイテムであり、これらが管理できないと人や設備に対するムリ・ムラ・ムダが発生します。QCDは製品におけるアウトプットのアイテムであり、これらが管理できないと不良品・原価高・納期遅延などが発生します。
4Mの管理の結果が、QCDそれぞれの要素の改善に反映されます。インプットである4Mの “要因管理” とアウトプットであるQCDの “結果管理” の両方を意識することが、生産管理の実効性を上げるために有効であり、QCDの最適化を実現することに繋がるのです。
■「4M」×「QCD」管理
Quality | Cost | Delivery | |
Man | 作業員のスキル | 労働生産性 | 正味作業比率 |
Machine | 工程能力 | 設備生産性 | 正味生産時間 |
Material | 品質劣化 | 購買活動 | 在庫回転率 |
Method | 作業手順書 | 加工条件 | 検査・測定方法 |
■「4M」と「QCD」の関係
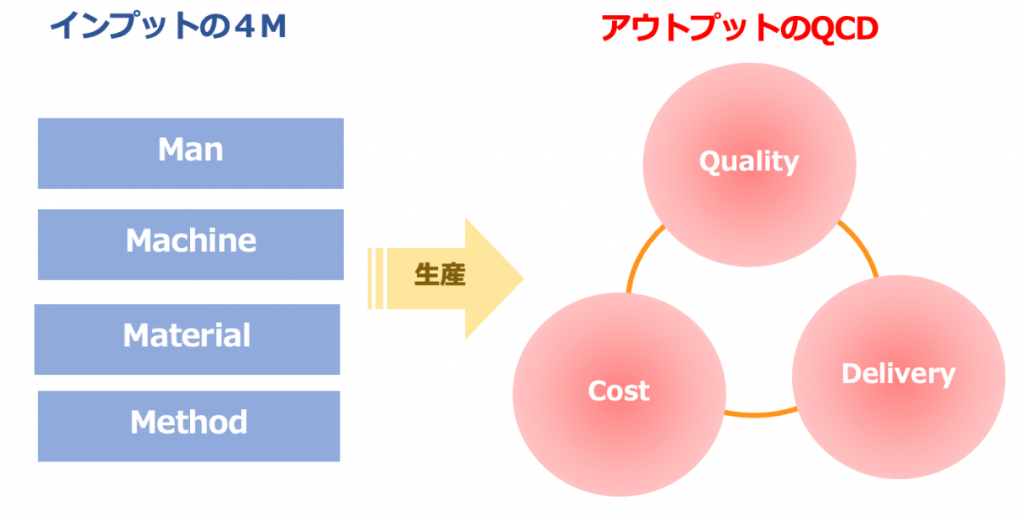
生産管理のスタートは「見える化」から
生産現場では、様々なことが「見えない」ことにより、計画通りに生産高が上がらない、利益が出ない、顧客に迷惑をかけるなどの問題が生じます。何も見えない状態では、どのような改善策を取ったら良いのか判断がつきません。
生産管理のスタートは「見える化」にあります。調達、生産、進捗、在庫、不良など、工場経営に必要なすべての項目を見えるようにする必要があります。工場の「今」を瞬時に把握できる状態にしておくことが理想です。そのために、変化の兆候を数字から把握します。計画と実績の乖離を把握して、その傾向や過去との比較から原因を突き止め改善策を打ちます。見える化は、改善という行動を促すためのトリガーと言えるでしょう。
生産管理の業務の3本柱はPlan、Do、See
繰り返しになりますが、生産管理の重要なポイントは3つあります。1つ目は、高品質なものをコストを抑えて短期間で製造することが目的であり、その肝はQCDの最適化を実現することであること。2つ目は、生産に関する “入” (受注)から “出”(出荷) までの工程全般をマネジメントの範囲とすること。3つ目は、「ものの流れ」のみならず「お金の流れ」という広い視点で管理を行うことです。このように、「質」と「量」の両面において、企業経営の軸とも言える非常に重要な役割を担っているのが生産管理の業務です。
しかし、もしかしたら皆さんは生産管理者に対して、「もっと効率のいい計画を立てられないのか」、「いつも無茶な要求ばかりしてくる」、「現場を走り回っているだけだ」などと不満を持っていませんか。これは管理がうまく回っていない証拠です。管理レベルを引き上げていかなければ、この先、利益創出の機会を失っていくばかりだと言わざるを得ません。生産管理は、工場全体を俯瞰する司令塔です。ますます競争が激しくなる中、司令塔なくしては工場は漂流し、打ち合わせばかりが多い現場となり、やがて沈没します。生産管理は「やってもやらなくてもいいもの」ではなく、「必ず取り組まなければならないもの」なのです。
中小製造業の生産管理の業務
では、生産管理の業務を具体的に考えて行きましょう。業務を大きく分けると、「Plan:計画」、「Do:手配」、「See:統制」が3本柱になります。この3つが的確にできることによって、顧客のニーズを満たすことが可能となります。
■生産管理の業務
Plan | 過去の受注データや景気情報、季節的要因、顧客の生産計画に基づき予測する 注文内容・予測を元に生産計画を立てる 生産能力を算出し、治工具・必要機材の予算を出す 受注に対して見積書を出す 受注に対する納期回答を行う |
Do | 予算に応じた仕入れ先選定を行い、資材を調達する 生産能力に応じて人員や設備を手配し、生産の段取りを立てる 関係各部門と調整し、生産がスムーズに行われるようにサポートする 外注管理を自社工程の延長との視点で行う 製造を実施する |
See | 生産状況全体の進捗を管理し、優先順位を明確化させるとともに納期調整を実施する 工程保証結果を確認し、品質の維持と改善を行う 製造・調達、購買計画と連携しながら適正な在庫を持つ 各工程の予定工数と実績工数の差異収集・比較・分析を行う 計画からはみ出た異常を確認したら、生産計画を修正し最善の生産状態を維持する 納品後原価の集計を行い、見積もりとの差異を明確化させる |
このように生産管理の業務内容は、実に多岐にわたります。製造業には多くの職種が存在しますが、業務数の多さから見れば、生産管理はダントツと言えるでしょう。中でも厄介なのは、部門間の調整です。営業部門からは「早く納品しろ」、製造部門からは「いや、それは無理」。不良品が出たときは、責任のなすりつけあいになることもあるでしょう。そんな時、生産管理の担当者は各部門の意見を調整して適切な “落とし所” を見出していく必要があります。生産管理の担当者は、生産の進捗を見守っていればよいのではなく、全体のバランスを調整するといったスキルも必要になるのです。
生産管理と工程管理の違い
両者の違いを混同している人も多いかもしれません。違いは、ひとことでいうと「管理する範囲の違い」にあります。生産管理は、生産計画の立案から原材料の調達、設備や人材の手配、完成品の検品と出荷、在庫管理まで、生産全体が対象になります。そこには、もののマネジメントだけではなく、お金のマネジメントも含まれます。これに対し、工程管理は、工場における実際の製造工程のみが対象で、生産管理の範囲に含まれる一部の管理機能と考えて良いでしょう。
生産管理が「難しい」「きつい」と言われる理由
業務量の多さもさることながら、生産管理は複雑な仕事が多いことから徹底した管理が難しいと言われています。生産管理に取り組んでも、なかなか効果を上げられない企業が多いのは、そのためでしょう。担当者からも「難しい」「きつい」という声が聞こえてきます。だからといって、企業の利益に直結する管理業務なので手を抜くことは許されません。そもそも生産管理はどうして難しいのでしょうか。課題をあげてみましょう。
■生産管理の課題
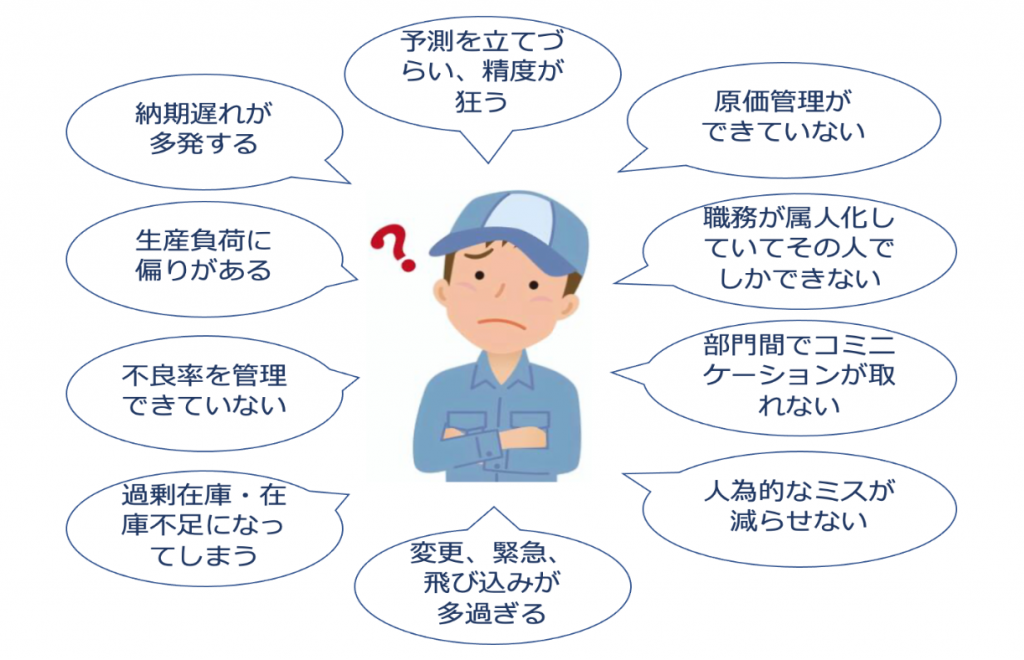
いかがですか?皆さんのところはいくつ当てはまりましたか?もしかして、10個全部というところもあるかもしれませんね。
確かに、「難しい」「きつい」内容が並んでいますが、例えば、部門間が互いに密な連携を取れば解決することが多いはずです。ではなぜ、部門間連携が取れないのか。それは、全体を俯瞰的に眺める管理機能が弱いからです。各部門の実情を把握し、全体最適を図る生産管理の機能を強化すれば解決する課題です。生産管理を行うためには、各業務の担当者が密に連携し、情報を共有しあうことが不可欠です(情報の一元管理)。とはいえ、担当者が必要な都度、いちいち関係者と連絡を取り、打ち合わせをしているようでは非効率極まりないでしょう。そこにシステムを活用すべき理由があります。
生産管理の課題を解決するにはシステムによる効率化で
生産管理は、手掛けていても実際は工程を管理する人が頭の中で行なっていたり、Excelで管理している企業が多いのではないでしょうか。「見える化」対策として、他にも企業ごとに様々な創意工夫がなされていることでしょうが、果たしてベストプラクティスになっているでしょうか。「井の中の蛙」になっていませんか。
複雑な生産管理を緻密かつ効果的に行なうためには、システムを用いて課題を解決していかなければなりません。生産管理システムについて詳しく知りたい方は、以下のURLから読み進めてください。

コメント