メルマガ「DXナビゲーション」バックナンバー:第22号 生産管理システムで「見える化」を実現する

「見えない」ことで起こる問題
中小企業の生産現場では、さまざまなモノが「見えない」こと(情報や状況が可視化されていないこと)により、計画通りに生産が進まない、品質にばらつきが出る、思ったように利益が出ない、納期遅れが生じる、在庫が過剰になるなどムリ・ムダ・ムラに起因する問題が日常的に発生しています。また、作業の進捗や作業者の負荷が見えない場合、リソースの配分が不適切になり、作業者が過度に負担をかけられたり、逆に仕事がムダに停滞することがあります。情報が共有されていない、あるいは見えない状態では、部署間やチーム間でのコミュニケーションが不足し、情報伝達の遅延や誤解が生じることもあります。これが原因で生産活動における連携が乱れ、全体のパフォーマンスが低下します。このような非効率が続くと、労働生産性が低下します。生産現場の状況がリアルタイムで、しかも一目で把握・共有できれば、急な受注や変更、納期短縮、不良、欠品といった突発的な事態にも迅速に対応できます。経営陣や管理職が、適切なタイミングで意思決定を行うこともできます。しかし、現実は、今、誰が、何をしているのか、何が起きているのか、現場の進捗状況がわからないといったことが往々にしてあるものです。
生産管理システムが必要な理由
このような課題を、IT技術を用いて解決するのが生産管理システムです。生産管理システムの「見える化」における役割は、製造現場の状況をリアルタイムで把握し、効率的かつ柔軟に対応するための情報を提供することです。生産管理システムでは、モノ、4M(Man=人、Machine=機械、Material=製品・材料、Method=作業方法)、QCD(Q:Quality=品質、C:Cost=コスト、D:Delivery=納期)、経営という各視点から、工場の生産状況を「見える化」し、生産工程に関わるすべての情報を一元管理します。手作業や人の介入といった属人的な要素を排除し、モノの情報や業務の情報をリアルタイムなデータとして収集・「見える化」することで、より効率的な生産活動と業務の最適化を実現するものです。
国内外の競争環境がますます厳しくなり、人手不足が深刻化する中で、生産性向上への取り組みの必要性は高まるばかりです。そのためには今こそ生産管理システムを導入し、そして既に導入済みの企業はさらに効果が高いシステムがないか見直していただき、現場、間接部門ともに、経験と勘とコツに頼るムダの多い工場運営を改めなければなりません。
加工機の性能が上がり、今以上に誰でも同じようにモノづくりができるようになれば、品質・納期などの「管理力」がものを言う時代になります。そのためには生産管理システムにより、いかにデータを活用し、QCDで差別化を図ることができるかどうかがポイントになってきます。
モノの「見える化」
生産現場のモノ、例えば、材料・製品・仕掛品・不良品・在庫などが見えない状況下では、探すムダ、手待ちのムダ、つくり過ぎのムダ、在庫のムダ、不良や手直しのムダなどが発生します。これらのムダは付加価値を生まない作業・業務であり、早急に無くす必要があります。
その中のひとつ、つくり過ぎのムダについて考えてみましょう。「不必要なモノを、不必要な時に、不必要なだけつくる」ことが、つくり過ぎのムダです。つくり過ぎのムダは、ムダの中でも一番悪いと言われており、早急に削減しなければなりません。つくり過ぎのムダが最も悪いとされる理由は、それが、在庫のムダ、動作のムダ、運搬のムダなど他のムダをも誘発させてしまうからです。また、つくり過ぎのムダを続けている限り、原価は下がりません。品質の低下にも結びつきます。後工程が困らないように在庫を大量に持つことは良い事でしょうか。いや、各工程がそれを実行したら工場の中は在庫品であふれかえってしまうでしょう。性能が優れ、高価な機械だから、使わなければ損だと判断して、必要数を無視してつくり過ぎてしまうことはありませんか。それもムダです。生産管理システムを用いて、必要なものを、必要な時に、必要な量だけ、しかも必要な時間で生産する仕組みを構築するとともに、常に在庫を「見える化」し、把握できるように管理しなければなりません(情物一致)。
4Mの「見える化」
4Mとは、Man(人)、Machine(機械)、Material(製品・材料)、Method(作業方法)の4つの要素を分析・改善していくことで、課題発見や問題解決を図る手法です。製造に関する生産性の良し悪しやトラブルなどは、すべてこの4Mが要因だと言われています。とりわけ、Manは、他の3Mすべてに大きな影響を与えるため、4Mの中でもっとも重要な要素だとされています。生産現場で発生する課題を解決するには、まずこの人の「見える化」をいかに行うか、工夫する必要があります。作業者の動きや作業時間、品質情報などを、生産管理システムを活用してリアルタイムに収集・分析し、問題や改善点を早期に把握することが求められます。
生産管理における人の「見える化」は、生産性向上や品質改善に貢献するだけでなく、作業者のモチベーション向上や作業環境の改善にもつながります。作業者が自分の作業時間や生産性が「見える化」されることで、自己評価や目標設定がしやすくなり、自らの生産性向上意欲を引き出します。
また、「見える化」ができていない組織では、業務内容を把握しているのが担当者のみという、いわゆる属人化が進みやすくなります。業務の標準化や平準化、リスクマネジメントの観点から、属人化した業務の「見える化」に取り組むことは必要不可欠であり、これも人の「見える化」を行う上での重要な点です。
さらに、作業者のスキルや能力の可視化も必要不可欠です。各作業者の教育・研修履歴、どの研修を受けたか、スキルや経験を一覧で管理することで、誰がどの作業を担当できるのかを把握しやすくします。これにより、最適な人員配置が可能になり、効率的な生産が実現できます。
QCDの「見える化」
QCDは生産管理において重要な指標です。QCDを管理して、品質の向上、コスト削減、納期達成率の向上などを実現することは工場管理の基本です。そのためには、生産管理システムの導入で、現場の作業者の動きや機械の稼働状況、作業進捗状況などをリアルタイムで「見える化」することで、生産ラインの全体像を把握することが必要です。そして、生産計画と生産実績の対比から、計画通りにモノづくりが進んでいるのかどうか、さらに、工程毎・設備毎にブレイクダウンして、生産ラインのボトルネックがどこにあるのかを把握しなければなりません。こうしたさまざまな情報が数値化、「見える化」された環境を構築することで、QCDの最適化を目指すことができます。
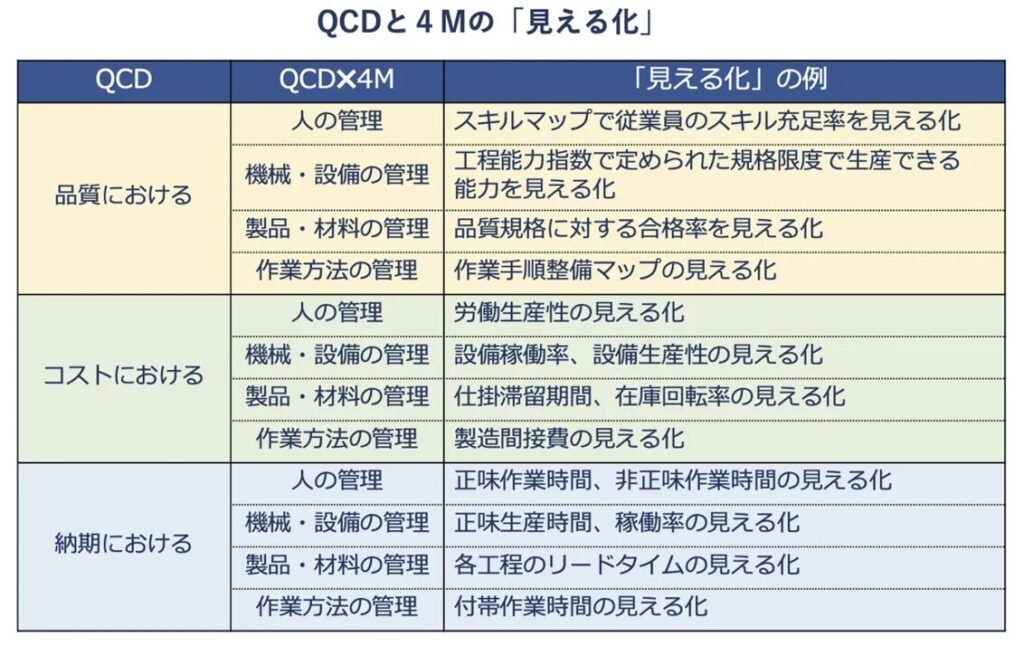
経営の「見える化」
中小企業では規模が小さいため、社長と従業員間、従業員同士の関係が密接であり、相互理解ができている、つまり「見える化」ができていると考えがちです。しかし実際は、ビジョンや経営方針は社長の頭の中だけにあり、従業員に十分に伝わっていないことは多いものです。従業員は程度の差こそあれ「うちの社長は何を考えているのかよく分からない」と感じているのではないでしょうか。
また、従業員も自分の目先の業務遂行で精一杯で、会社全体の動向や他の従業員の様子に関心を寄せる余裕がないという事態もみられます。自分の周囲のことしか見えない状況下では、自工程さえ良ければよいとなりがちで、部分最適に終始してしまいます。工場全体の最適化を図り生産性を向上させるためには、経営の「見える化」によって、社長が迅速な意思決定を行うとともに、その想いを従業員に伝え・共有することが何よりもまず優先されるべきではないかと思います。
まとめ
モノづくりの現場での見える化の目的は“見える”だけではなく、“見える”ことにより、どのような異常が起きているのかを把握し、そのための対策を考え、是正処置をとっていくことです。強い企業であり続けるためには、全社的にPDCA(Plan-Do-Check-Action)サイクルを回し続ける必要があり、PDCAサイクルを回すためには見える化ができていなければなりません。見える化を通じて、進捗や問題点、改善点を明確に把握できるようにします。
企業の現場では各部門がそれぞれの業務にさまざまなデータ集計や分析を実施していますが、多くの場合、これらの作業を手作業や表計算ソフトを駆使して行っているため、部門間で情報共有の食い違いや精度の問題、属人化が起こりがちです。その都度、特定の人を介してデータを精査し直さなければならない、ということが起こっているのではないでしょうか。受注から生産、品質管理、在庫、出荷までのデータを一元的に管理できる生産管理システムを、全社員が1人1台で有効に活用することによってこそ(受発注機能だけといった単機能のシステムでは意味がありませんし、特定の人間しかシステムに触れることができないのでは効果が限定的です)、スムーズに、タイムリーに見える化を実現できます。
コメント