メルマガ「DXナビゲーション」バックナンバー:第8号 標準なきところに改善なし

標準化は皆さんの関心が高い!
昨年ホームページの記事に「製造業における標準化とは?標準化の基本から進め方まで徹底解説!」をアップしたところ大きな反響を呼び、以来1年近く経つ現在までたくさんの皆さまに読まれてきました。ご拝読、ありがとうございます。
つきましては今回はメールマガジンにて続編を記したいと思います。ホームページの記事を読まれていない方は併せてご覧いただければ幸いです。
標準化とは?
皆さんの会社の業務には“正解”(決まったやり方と管理数値)はありますか?後輩に仕事を教えていて、「今Aさんに教わったことは、この前Bさんに教わったことと内容が違いますが…」「人によって言うことが違いますが、どれが正しいのでしょうか?」と言われた経験はありませんか?
これは、「やり方が決まっていない=業務が標準化されていない」から起こることです。標準化とは、社員全員が同じ成果を出せるように業務の進め方とQCDに関する管理数値を決め、設定したルール・数値に適うように業務を実施することを指します。標準化を推進することで業務の流れや手法が統一され、業務効率が上がり、担当者ごとに業務品質のばらつきを解消することができます。
標準化における重要な概念として「再現性」と「代替性」が挙げられます。
再現性:業務を同じ作業手順で行えること
代替性:担当者が違っても同じ水準で作業を行えること
標準化を進めることで業務の再現性と代替性が担保され、正しい作業手順に沿って業務を行うことで誰でも一定の業務が遂行できるようになるため、一部の社員に業務が依存している状態(属人化)を解消し、社員の負担を軽減することができます。
標準化されてないと正常と異常の区別がつかない
標準化が明確であり、正常と異常の区別ができないと、何が問題なのかが分かりません。それでは改善の手を打ちようがありません。そのためには正常と異常の境界線(管理限界=あらかじめ定めた管理の幅)がどこにあるのか、そして現在はどのレベルにあるのか見極められるようにしておくことが重要です。その際、数値化できるものは、できるだけ具体的に数値化しておかなければなりません。境界線がどこにあるのかわかっていて、異常や変化に気がついた時に素早く手を打てれば、不具合や不良の発生を事前に防止できる可能性が高いのです。
逆に、いつもと違うぞ、おかしいぞという意識を持てなければ、不具合や不良をやり過ごしてしまいます。小さな異常に気づかず放置しておくと問題は大きくなります。正常な状態を正しく把握していることが、異常管理の第一歩となります。
よく「問題がないことが最大の問題だ」と言われますが、これは正常な状況にしようという目標がないために問題に気づかないとも言えます。どこの工場、どこの部門も適切な目標管理を行えば、必ず異常はあるはずです。目標がないため、異常に対する認識が欠如してしまっているのです。感度を上げて異常を察知できるようにしなければなりません。「異常なし」という職場ほど、問題が多いと思うべきでしょう。
「良い標準化」と「悪い標準化」
標準は一度定めてしまえばそれでお終いではありません。皆さんの工場で作業標準(マニュアル)を見せていただくと、たびたび改訂されている現場と、初版が発行されて以来一度も改訂がされていない現場があります。作業標準をどれだけ見直し改訂しているかは、改善をいかに進めているかの度合いとも言えるのではないでしょうか。
自社を取り巻く環境も、顧客の環境も、社会環境も常に変わりますので、作業標準を変えた方が業務効率とQCDの向上につながると判断した時点で、それをより良いものへと改訂していく必要があります。現状にいつまでもこだわって変更しない標準化は「悪い標準化」です。今よりも良い方法が考えられるならば、都度タイムリーに改定し、新たな標準に作り変えるというのが「良い標準化」です。改善が積極的に進む現場は、標準の改訂は当たり前のこととしています。標準の定期的なチェックを欠かさず、内容を進化させて行きましょう。
「標準なきところに改善なし」
繰り返しになりますが、標準化は、属人化の排除、効率の向上のほかに、ムダムラムリを見つける、正常と異常を区別する等、改善のツールとして活用することができます。トヨタ生産方式で「標準なきところに改善なし」と言われるように、標準化は、何が問題なのかを判断する基準になるのです。改善のためには、しっかりとした標準を定めて、それを守り、そしてPDCA(Plan-Do-Check-Action)サイクルを回していくことが重要です。
まずは作業を標準化してルール化・数値化する。そうすれば問題点が見えてきて、改善点を検討できるようになります。
標準化には生産管理システムの活用が重要!
属人化を解消し、部門間での情報共有や業務の一元管理を実現でき、業務改善や標準化に貢献する上で、生産管理の見える化は必要不可欠であり、そにためには生産管理システムは強力なツールとなります。具体的には、以下のような点で生産管理システムが業務の標準化に寄与しますので、製品の品質を安定させるだけでなく、工場全体の効率的な運用とコスト削減を図るために、システムを導入すべきです。
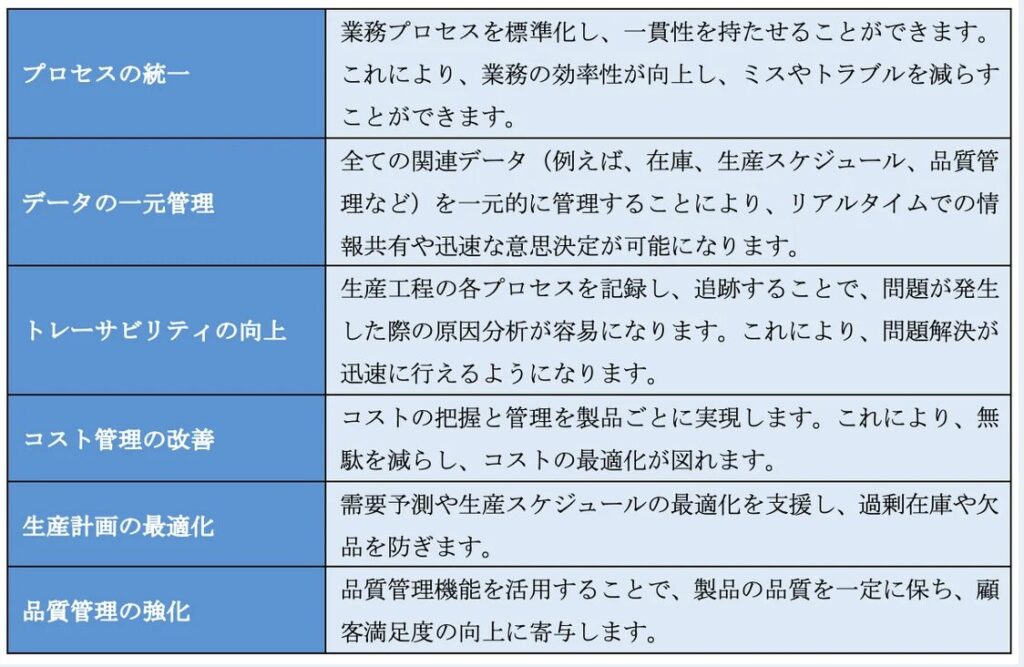
コメント